www.industrie-afrique-du-nord.com
25
'17
Written on Modified on
L'Unidrive M700 VSD permet à une grande centrale électrique d'optimiser les performances et de réduire les coûts de maintenance de ses tours de refroidissement
Cette centrale électrique utilise désormais des variateurs Control Techniques Unidrive M700 d'Emerson, pour commander 22 ventilateurs répartis dans deux tours de refroidissement. Se substituant à un système initialement installé en 1975, ces nouveaux variateurs apportent de nombreux avantages. On peut désormais faire varier la vitesse des ventilateurs pour minimiser la consommation électrique à faible charge ; éliminer la rotation sous l'effet du vent grâce à la présence d'un système de freinage ; minimiser le risque de givrage en hiver ; atténuer les vibrations des ventilateurs sans devoir les mettre hors-service ; et éliminer les réglages de pales saisonniers pour éviter les surcharges moteur en hiver et le manque de débit en été. Rien que l'élimination des réglages de pales se traduit par une économie substantielle de main d'œuvre estimée à 38 000 dollars par an.
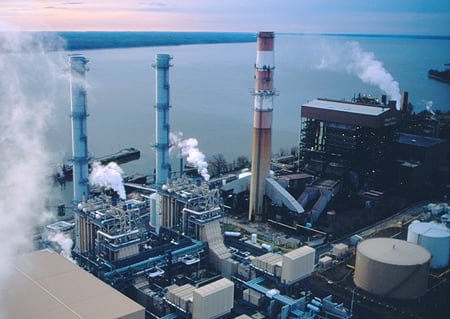
Réduction des coûts et de la consommation, sans impact sur le rendement des tours
• Gérer la consommation d'énergie et la capacité de refroidissement impliquait de pouvoir allumer ou éteindre les moteurs 200 cv des ventilateurs, qui jusqu'ici tournaient en permanence à vitesse maximum. La capacité à faire varier la vitesse des ventilateurs, et donc le refroidissement, en fonction de la charge permet à tous les ventilateurs de tourner en consommant beaucoup moins d'énergie (pour un rendement optimum des tours). Le système ne déplace que le volume d'air nécessaire à l'évacuation de la chaleur et cela se traduit par une consommation beaucoup plus faible.
• Pour contrôler les vibrations certains ventilateurs devaient être arrêtés, même en cas de charge importante et donc de besoin de refroidissement élevé. La capacité à maintenir tous les ventilateurs en fonctionnement, dont certains à vitesse réduite pour éviter les vibrations, assure un refroidissement optimum lorsque c'est nécessaire.
• L'autre sujet était le besoin de réglage saisonnier manuel du pas (inclinaison) des pales de ventilateur, pour prendre en compte la différence de densité de l'air entre les mois d'été et les mois d'hiver. Cette seule opération demandait près de 480 heures de main d'œuvre par an, qui représentaient un transfert significatif des ressources de maintenance au détriment de tâches plus urgentes au sein de la centrale, plus des coûts de location de grue et de gestion de sécurité indispensables à la réalisation de ces réglages saisonniers.
Gestion et protection des investissements
• Les ventilateurs sont équipés d'un arbre d'entraînement en fibre de verre et métal de 16 pieds (près de 5m) de long, reliant le réducteur du ventilateur au moteur. En l'absence de système de freinage, la rotation des ventilateurs sous l'effet du vent était un problème constant, qui pouvait parfois nuire au démarrage ou imposer des surcharges aux moteurs, générer des torsions sévères de l'arbre d'entraînement, et parfois même des problèmes au niveau des réducteurs. Avec le nouveau système, des fonctions de démarrage progressif et de freinage-avant-démarrage font partie des capacités standard du M700 VSD.
Ces fonctions de démarrage progressif et de freinage-avant-démarrage minimisent le couple de torsion subi par l'arbre d'entraînement lors du démarrage du ventilateur, et éliminent les problèmes liés à la rotation sous l'effet du vent. Les moteurs ne voient jamais un courant élevé appliqué au moment du démarrage.
• Le givrage et le dégivrage sont des problèmes majeurs pour les tours de refroidissement. Le système existant nécessitait de mettre les ventilateurs en rotation inverse si de la glace se formait sur les parois des tours, pour tenter de dégivrer la charge au niveau de l'admission des tours. Ceci aurait pu avoir des conséquences très graves, pouvant aller jusqu'à l'effondrement des tours. Une circulation d'air bien gérée par temps froid grâce à la capacité de vitesse variable permet d'éviter le sur-refroidissement, qui entraîne le givrage. Cela évite d'avoir à inverser le sens de rotation des ventilateurs, sauf en cas de conditions climatiques extrêmement défavorables.
« Nous avons décidé d'étudier les solutions VFD (Variable Frequency Drive, ou variateur à fréquence variable) et trois constructeurs ont été envisagés au départ, » déclare Mark Leigh, Conseiller Technique pour le fournisseur d'énergie. « Cependant, Control Techniques [du groupe Emerson] était le seul en mesure de tenir les délais de livraison très courts dont nous avions besoin pour ce projet. Ils se sont aussi révélés très compétents techniquement pour nous recommander une solution optimisée. »
Des variateurs AC Unidrive M700 de Control Techniques à capacité Ethernet temps-réel ont été installés dans une salle de contrôle de la centrale, et pilotent désormais 22 ventilateurs de tours de refroidissement. Ces variateurs offre un haut niveau de performances et permettent un contrôle très souple des moteurs à induction et des moteurs à aimant permanent. Le plus important pour la centrale est que les nouveaux Unidrive M700 offrent un meilleur contrôle du processus.
« Dans le cas d'un moteur de ventilateur classique branché en direct, les variables sont le pas des pales et la densité de l'air, avec une puissance maximum fixe à vitesse fixe, en l'occurrence 1750 t/mn, » explique M. Leigh. « En revanche, les variables dans le cas d'un moteur de ventilateur à commande VFD, sont la vitesse de rotation et la densité de l'air, avec une puissance maximum fixe et un pas de pale de ventilateur fixe. Cela ne coûte donc rien en main d'œuvre de régler la vitesse, puisque ceci est assuré automatiquement grâce la commande VFD dans la limite des 200 cv, qui sont la puissance nominale maximum du moteur et du démarreur. Nous estimons l'économie à environ quatre personnes pendant trois semaines, soit environ 480 heures de main d'œuvre, soit approximativement38 000 dollars par an. »