www.industrie-afrique-du-nord.com
14
'14
Written on Modified on
Plus de fonctionnalités, moins d’ingénierie
Bosch Rexroth développe des fonctions préprogrammées pour réduire le temps d’ingénierie nécessaire à l’automatisation et faciliter le paramétrage des machines.
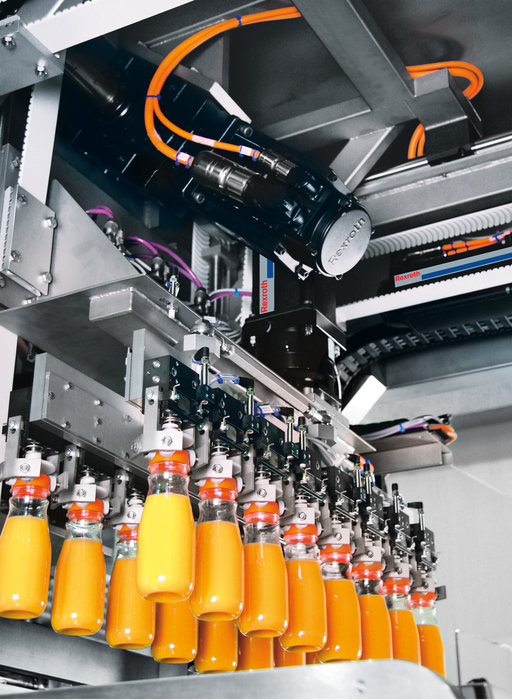
• Un temps d’ingénierie réduit accélérant la mise sur le marché
• Des fonctions préprogrammées pilotables à distance ou via le réseau IT
• Des machines plus modulaires grâce à l’entraînement sans armoire
Dans l’agroalimentaire, les utilisateurs de machines ont besoin de systèmes très flexibles pour coller à l’évolution rapide des tendances de consommation. Cette demande implique le recours de plus en plus fréquent aux servomoteurs et aux fonctions numériques. Une complexité pour les fabricants de machines. Bosch Rexroth propose désormais Open Core Engineering, une interface dotée de fonctions préprogrammées qui apporte une grande souplesse à chaque fonctionnalité de la solution système IndraMotion. Par ailleurs, son entraînement sans armoire IndraDrive Mi permet une approche modulaire de la machine. Grâce à ces solutions, les fabricants peuvent ainsi réduire l’ingénierie nécessaire à l’automatisation et accélérer la commercialisation de leurs machines.
Paramétrer au lieu de programmer
Open Core Engineering comprend tous les outils logiciels nécessaires à une ingénierie efficace. Rexroth a intégré au logiciel des ensembles de fonctions préprogrammées incluses dans la solution systèmes IndraMotion. Par exemple, les systèmes dits « adaptatifs » ajustent la machine aux changements de conditions sans aucune programmation supplémentaire. Grâce à la réduction des vibrations des servomoteurs intelligents, les entraînements électriques IndraDrive augmentent la dynamique du mouvement tout en épargnant le système mécanique et en empêchant le débordement des contenus. Ce contrôle des mouvements accroît la productivité et compense automatiquement les fluctuations de paramètres des processus. Le fabricant de machines n’a plus qu’à paramétrer cette fonction déjà préparée.
La fonction profils de cames FlexProfile réduit le temps de développement nécessaire aux changements de format et de recette, simplement depuis le programme applicatif. Cette fonction établit automatiquement les relations de mouvement entre des entraînements connectés. Il suffit au constructeur de définir des paramètres pour augmenter la flexibilité des machines.
Le recours croissant au contrôle numérique pour la mise en œuvre de fonctionnalités sur les machines augmente la modularité, à condition que les logiciels soient eux-mêmes modulaires. Le modèle de programmation GAT (Generic Application Template) de Rexroth illustre cette tendance. Cet outil d’ingénierie permet de créer et de lier rapidement des modules logiciels entre eux pour former des solutions d’automatisation complètes. Avec l’augmentation de la part du logiciel dans les machines, les fabricants peuvent ainsi réduire leurs délais de commercialisation.
Innover grâce à des fonctions personnalisées
Les constructeurs de machines peuvent également réaliser des fonctions spécifiques en accédant eux-mêmes en temps réel aux langages informatiques les plus avancés, grâce à la nouvelle interface Open Core Engineering. Cette innovation Rexroth permet un accès étendu au noyau de commande (lire le communiqué Open Core Engineering).
Grâce à la création d’applications sur des terminaux mobiles (smartphones, tablettes), Open Core Engineering simplifie les opérations, les diagnostics et l’accès aux commandes à distance.
La technologie d’entraînement sans armoire simplifie la modularité
Côté matériel, l’entraînement sans armoire IndraDrive Mi facilite la modularité des machines. En rassemblant en une seule unité l’électronique d’entraînement et le moteur, l’électronique de l’armoire de commande est presque entièrement éliminée, et le câblage nécessaire à la connexion des différents composants considérablement réduit. Il en résulte un maximum de flexibilité et d’efficacité à la fois pour le fabricant et l’utilisateur de la machine : la taille, le câblage et la consommation d’énergie de l’armoire de commande peuvent être réduits jusqu’à 90 %. Un seul câble est nécessaire pour la connexion des entraînements, reliés en série. Si des entraînements supplémentaires sont requis ultérieurement dans le système, pour installer un module complémentaire par exemple, ils peuvent être facilement intégrés à l’emplacement souhaité dans la ligne de production, sans affecter l’armoire de commande ni le reste de la machine ou de la ligne.