www.industrie-afrique-du-nord.com
25
'20
Written on Modified on
Cinq étapes pour maintenir l’automation
Une haute performance et le débit obtenus grâce à la mise en œuvre des processus automatisés sont un avantage clé pour les fabricants qui envisagent d’abandonner les solutions manuelles traditionnelles. Le temps d’arrêt dû à une maintenance prévue ou imprévue peut rapidement réduire le rendement si les processus de production sont suspendus trop longtemps. Chaque seconde de temps d’arrêt de la ligne de production automatisée entraîne des coûts qui peuvent rapidement se traduire par des sommes importantes. Dans le présent article TME .
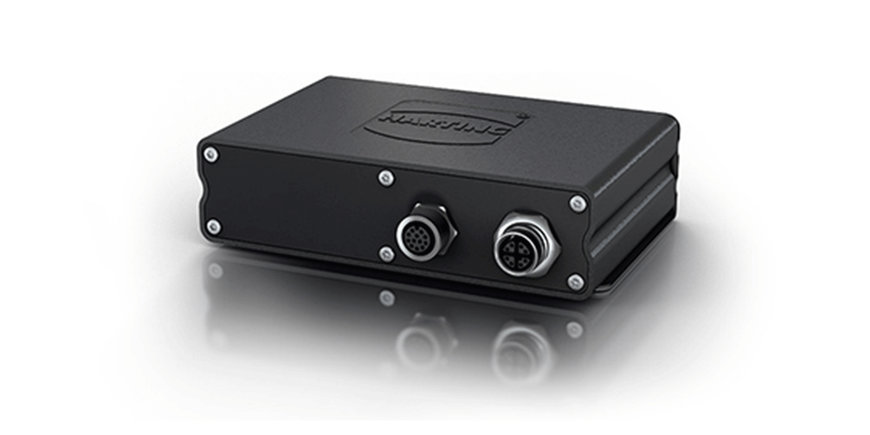
L'automatisation moderne modifie les méthodes de production actuelles. L'idée de l'Industrie 4.0 et d'Internet des objets industriel (IIoT) deviennent de plus en plus attrayantes et les producteurs commencent à profiter de l'utilisation de techniques de production intelligentes (graphique 1). L'IIoT et l'Industrie 4.0 sont basés sur la communication machine-machine, le travail dans le cloud et sur une série de composants électriques d’automation, de capteurs et d’actionneurs – tous les composants contribuent à une plus grande efficacité des processus. Avec l’augmentation du nombre de composants dans l’usine de production, le nombre de composants qui nécessitent une sélection, une inspection et une maintenance appropriées augmente également sans précédent.
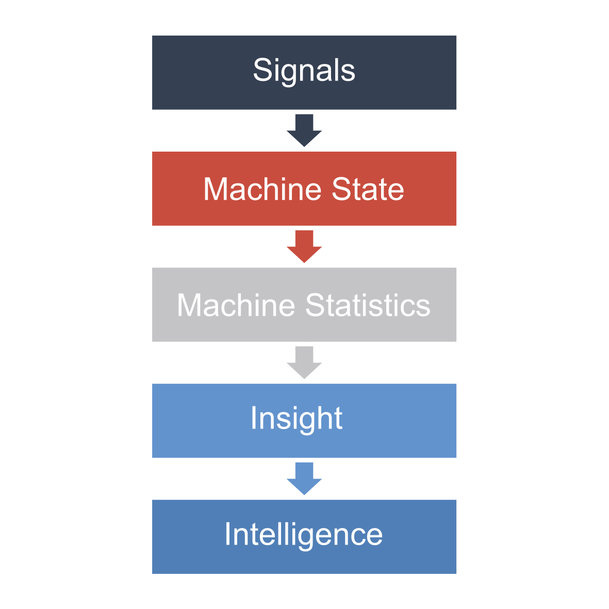
Les solutions de l’Industrie 4.0 donnent aux ingénieurs plus de connaissances de sorte qu’ils soient en mesure de mettre en œuvre des systèmes intelligents de maintenance prédictive pour minimiser le temps d’arrêt.
Étape 1. Envisager la stratégie de maintenance
Une bonne maintenance des lignes automatisées est nécessaire pour maximiser le temps de travail et pour maintenir les coûts bas. D’habitude, dans les usines de production trois stratégies de maintenance sont appliquées en ligne technologique :
Maintenance réactive
La maintenance réactive est une approche non planifiée qui vise à réparer régulièrement les machines et les composants au moment de la panne et l’opérateur ne sait pas quand cela peut se produire. C’est une approche courante parce qu’elle est apparemment la moins chère. Lorsque le processus est réalisé sans difficultés, il génère les coûts minimes – mais il arrive rarement que tout cela se déroule sans difficultés ! Dans une grande usine il est très probable qu’un élément de l’équipement doit être entretenu à un moment donné. Lorsqu’il est endommagé, les effets peuvent être catastrophiques et la réparation coûtera cher.
Maintenance préventive
La maintenance préventive contrairement à la maintenance réactive est une approche planifiée. Elle comprend les contrôles réguliers de l’équipement pour prévenir toute panne et réparer les pièces usées avant l’apparition des dommages coûteux. La maintenance planifiée et régulière basée sur les cycles moyens de vie des machines réduit également les coûts de réparation en cas de panne et les coûts de travail associés. De plus, elle prolonge la durée de vie des appareils critiques en contribuant à la réduction des frais d’exploitation totaux et à l’amélioration des performances. Il a été prouvé que les stratégies de maintenance préventives apportent un meilleur retour sur investissement par rapport à la maintenance réactive.
Maintenance prédictive
La maintenance prédictive – également connue sous le nom de maintenance intelligente – est une autre forme de maintenance planifiée pour laquelle les usines de production utilisent la technologie de prévision lorsque les appareils tombent en panne et d’entretien des appareils avant l’apparition de la panne. Grâce à la maintenance prédictive chaque ingénieur peut être parfaitement préparé à faire un bon travail à un bon moment et en utilisant les pièces appropriées pour minimiser le temps d’arrêt.
La plupart des stratégies de maintenance prédictive sont basées sur les capteurs, sur les systèmes de mesure et sur les logiciels de machine qui surveillent et suivent les performances d'une ligne automatisée. Cela permet aux ingénieurs de contrôler des performances de leurs machines et de prévoir une défaillance potentielle en évitant ainsi les temps d'arrêt inattendus.
Les systèmes de maintenance prédictive correctement mis en œuvre présentent plusieurs avantages. Comme les stratégies préventives, elles prolongent le cycle de vie et le temps d’un bon fonctionnement des machines. Elles permettent également aux ingénieurs de gérer plus efficacement les équipes de service et contribuent à des économies de coûts.
Étape 2. Envisager les sources d’alimentations de secours
Quelle que soit la maintenance, planifiée ou non, il est important d’avoir une source d’alimentation de secours, comme par exemple les alimentations sans coupure (UPS). Les coupures d’alimentation inattendues ainsi que les coupures de courant et les chutes de tension peuvent provoquer la perte de contenu du disque dur ou les dommages aux composants en entraînant des changements irréversibles ou les pertes. Les alimentations UPS, telles que celles fabriquées par Eaton, sont utilisées pour alimenter les composants d’automation et de contrôle sensibles, des postes de travail, des centres de gestion des processus technologiques ou pour le traitement des données industrielles.
Elles permettent d’arrêter en toute sécurité des lignes et des appareils d’automation en protégeant simultanément les données clés contre une panne de courant imprévue.
Étape 3. Choisir un équipement fiable
Premièrement il est nécessaire de choisir un équipement fiable qui convient à un objectif précis et à un environnement spécifique, ce qui est essentiel pour maximiser le temps d’utilisation. Par exemple, avec le développement de l’IIoT, l’utilisation des ordinateurs industriels devient plus courante. Ces ordinateurs peuvent traiter de grandes quantités de données et de résister aux caractéristiques environnementales défavorables présentes dans les halls industriels telles que la saleté et l'humidité. Ces ordinateurs disposent de la mémoire flash avec le système d’exploitation installé utilisé par le client et d’autres applications utiles. L’ordinateur industriel HARTING (graphique n° 2) avec un port Ethernet et une mémoire flash de 32 Go est une solution idéale. La classe d’étanchéité IP67 garantit une excellente protection contre la saleté et l’humidité.
Étape 4. Choisir les bons outils
Pour minimiser le temps d’arrêt, il est nécessaire d’utiliser les bons outils de travail. Dans chaque système de maintenance les ingénieurs doivent disposer d’un équipement approprié pour une tâche précise pour qu’ils puissent effectuer la maintenance rapidement et efficacement. Il existe de nombreux outils et instruments de mesure destinés aux travaux spécifiques. Par exemple, un tournevis simple sera-t-il suffisant ? Ou bien il serait mieux de choisir des outils électriques qui permettent au personnel de maintenance d’effectuer une tâche plus rapidement et ainsi de gagner un temps précieux ? Il faut s’assurer que le kit de maintenance comprend tous les éléments de base ainsi que ceux plus spécialisés qui sont nécessaire pour effectuer la réparation spécifique.
Le kit doit inclure les outils de maintenance de base qui permettront de minimiser le temps d’arrêt
Étape 5. Assurer un accès facile aux pièces de rechange
Il est indispensable d’assurer un bon fonctionnement des systèmes qui permettent un accès rapide aux pièces de rechange appropriées. Sans aucun doute, les systèmes utiliser pour passer les commandes faciles à utiliser et à gérer s’avéreront utiles. Par exemple, l’interface de programmation d’application (API) utilisée par TME permet aux ingénieurs d’optimiser le processus d’achat. Un outil convivial pour l’utilisateur signifie que les ingénieurs passent moins de temps à choisir la bonne pièce pour réparer la machine, de sorte qu’ils puissent rapidement restaurer l'efficacité d'une ligne de production automatisée. TME est un distributeur officiel de nombreuses marques leader dont les composants électroniques et passifs permettent d’automatiser et de transformer les processus de production – entre autres Eaton, Panasonic, HARTING et Omron. Le niveau de stock est mis à jour en temps réel de sorte que les ingénieurs savent précisément combien de pièces sont actuellement disponibles et les prix de chaque produit peuvent également inclure les remises individuelles ou être exprimés en devises différentes. Cet outil combiné à un support technique permet aux ingénieurs de trouver rapidement les composants dont ils ont besoin.
Conclusions
La maintenance est essentielle pour maintenir la compétitivité des lignes de production automatisées modernes et pour garantir qu’elles fonctionnent de manière la plus efficace et la plus rentable possible. Les distributeurs coopérant avec les clients proposant une haute disponibilité et les livraisons rapides des composants clés et de matériaux consommables peuvent aider à minimiser le temps d’arrêt. Le fait de permettre la commande directe des composants clés à l’aide d’une interface de programmation d’application (API), comme celle proposée par TME, peut encore augmenter les performances et réduire le temps d’arrêt. En la combinant avec la maintenance prédictive intelligente il est possible d’atteindre encore plus d’avantages et de maximiser les performances. Le processus efficace qui minimise le temps d’arrêt accéléra le retour sur investissements coûteux qui sont basés sur l’automatisation la plus rapide de la production Pour plus d’information sur TME et sur l’API proposée, visitez le site web https://developers.tme.eu/en.
www.tme.eu