www.industrie-afrique-du-nord.com
05
'12
Written on Modified on
Rapidité de livraison: Respect du planning de production grâce à l’optimisation de la gestion des pièces
Fischcon PV, le fabricant néerlandais de distributeurs hydrauliques et de systèmes de lutte contre l’incendie utilisés pour l’exploration pétrolière et gazière, s’est aperçu que la création d’un processus transparent dévolu à la gestion de l’approvisionnement des pièces autorisées accélérait le traitement des commandes et comportait de nombreux avantages client.
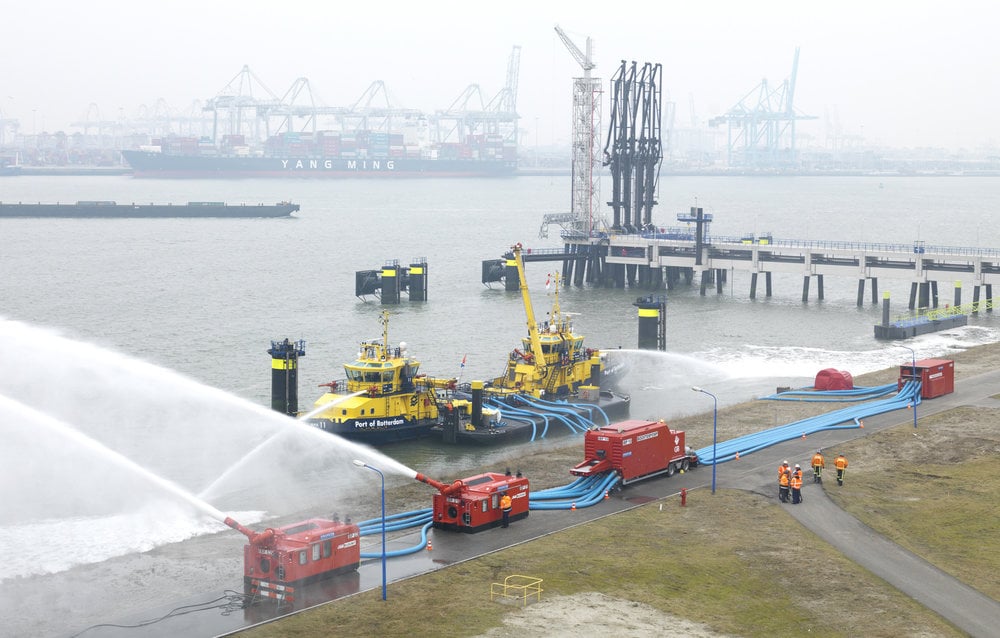
La commande de grandes pièces comme des moteurs électriques et les pompes prend souvent beaucoup de temps. La fabrication ne peut démarrer tant que toutes les pièces ne sont pas réunies sur place. Tout retard important de production expose l’entreprise à des pénalités. Le cœur de la stratégie d’approvisionnement rationnalisé repose sur une base de données centralisée des pièces, créée voici deux ans dans le système mécanique PDM utilisé par l’ingénierie mécanique en interne. Les ingénieurs électriciens de Fischcon travaillent dans EPLAN. L’installation d’une interface réalisée par EPLAN a établi une connexion EPLAN/PDM bidirectionnelle qui leur permet d’accéder à la base de données. En conséquence, tous les départements ont accès à la gestion des pièces.
L’interconnexion EPLAN/ERP/PDM fait gagner du temps et évite les erreurs
Grâce à l’utilisation de ce système intégré pour commander au plus tôt les matériels appropriés, Fischcon a pu livrer les commandes plus rapidement, en limitant grandement les risques de conception ou les erreurs d’achats. «L’interconnexion entre l’ERP, le PDM et EPLAN permet d’éviter les mauvaises communications et les flux de papiers inutiles, explique Pascal van der Jagt, Directeur de l’ingénierie. Nous pouvons vérifier immédiatement si nous avons toutes les pièces nécessaires sous la main. Commander la mauvaise pièce est quasiment impossible». La base de données renferme environ 15 000 pièces. Pour l’exécution d’une commande, on établit une seule et même facture couvrant l’ensemble des matériels, du plus petit boulon au moteur Diesel ou électrique, au lieu de plusieurs factures distinctes pour chacun des secteurs de l’ingénierie. La réalisation d’une seule liste de nomenclatures facilite la reconnaissance des achats et les délais de dépannage avant qu’ils ne posent de sérieux problèmes.
Une gestion active payante
La base de données est gérée de façon active, ce qui, selon Pascal van der Jagt, compense largement son coût. Ainsi, l’ensemble des données relatives aux pièces est précise, à jour et au format standard. La centralisation a également permis de relier la gestion des pièces à la gestion des révisions. «Dès qu’une révision de conception s’impose, les commandes peuvent être annulées automatiquement et les pièces de remplacement adéquates commandées, souligne Pascal van der Jagt. Les gains de temps, à cet égard, sont énormes».
Conception rationnalisée des schémas P&ID dans EPLAN PPE
Il y a tout juste un an, la société a commencé à utiliser EPLAN PPE pour standardiser et accélérer la création des schémas tuyauterie et instrumentation (PID), d’où également des approbations clientèle et des commandes de pièces plus rapides. «Nous pouvons considérablement raccourcir le temps de traitement, souligne Pascal van der Jagt. Une fois le PID approuvé par le client, il n’y a qu’un petit pas à franchir pour concrétiser la liste complète d’équipement, instrumentation et tuyauterie. Nous pouvons commander les principales pièces plus rapidement».
La gestion standardisée des pièces, une situation «gagnant-gagnant»
Aujourd’hui, Fischcon est en mesure de produire plus rapidement des devis de projet précis et de fournir à ses clientèles des documents dans un format cohérent, qu’il s’agisse du schéma PID, de la nomenclature, de la liste d’équipement, instrumentation et tuyauterie, ou de la documentation détaillée jointe au travail terminé.
La gestion centralisée des pièces se traduit par des économies directes non négligeables pour l’entreprise. Pour l’un de ses plus gros systèmes, le temps passé à traiter les commandes a diminué unitairement d’environ 500 heures, soit une amélioration de 20% correspondant à une économie annuelle de l’ordre de 150,000 €.
Illustrations
File: Spuitwagens.jpg
Légende: Essai d’un système de lutte contre l’incendie dans le port de Rotterdam
File: Spuitwagens:staand_beeld.jpg
Légende: Essai d’un système de lutte contre l’incendie dans le port de Rotterdam
File: Blauwe_box.jpg
Légende: conception technique 3D d’un distributeur hydraulique